LOS Series
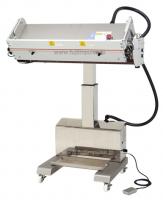
Electric / Temperature Controlled Impulse Sealer for Large Size Packaging
Temperature Controlled Seal for Large Size Packaging
Photo of LOS-1000



Main Features
Applications & Features | Extra-length sealer |
Operating method | Electric/air-cylinder operated |
Packaging type | Seal only |
Daily use frequency as model selection guideline | Up to 1,000 bags, electric/air-cylinder operated |
Bag size (max.) | 60cm (23.6 inches), 80cm (31.5 inches), 1m (39.4 inches), 1.2m (47.2 inches) |
Latest type | Type A |
Compatible packaging materials (total thickness of two or more sheets):
Double-side heating type
- PE : 0.4mm/15.7mil,
- PP : 0.3mm/11.8mil,
- NY : 0.3mm/11.8mil,
- PVA : 0.3mm/11.8mil,
- other laminated materials : 0.4mm/15.7mil
Double-side heating type
- PE : 0.6mm/23.6mil,
- PP : 0.4mm/15.7mil,
- NY : 0.4mm/15.7mil,
- PVA : 0.4mm/15.7mil,
- other laminated materials : 0.5mm/19.7mil
Standard equipped with heating-temperature control
Onpul
Setting the ideal sealing condition
The most prominent feature of the Onpul System is the ability to set and maintain the ideal sealing condition.
The heating temperature setting is made possible through the use of a high-sensitivity temperature sensor for temperature control, and a microcomputer controller.
You can now complete the heating process at just the right temperature for melting the film regardless of the air temperature or fluctuations in the machine temperature.
Seal heating temperature setting range: 60 to 250℃
Seal cooling temperature setting range: Between 40℃and the seal heating temperature. Note*
Note The seal-cooling temperature must be set at a value lower than the user-defined heating temperature setting. If the cooling temperature is set at a value too close to the heating temperature, cooling will not take place and result in the shortening of the life of some parts, including the Teflon part.
Easy-to-operate microcomputer controller
The selection and setting of work method and vacuum method, as well as of gas-flush method and its frequency, are all controlled at the microcomputer controller. Simply press the touch panel buttons for the settings.

Use of I-heating element
Use of I-heating element, which expands relatively little when heated, reduces the chance of the heating element breaking in the middle. Its use also prolongs the life of peripheral components such as the temperature sensor that comes in contact with the heating element.
Adjustable head height
The height of the head of the sealer can be adjusted to suit the package content by operating the buttons on the side of the machine.
- When the bag is set vertically to the head: 800 to 1370mm
- When the bag is set horizontally to the head:1020 to 1590mm



Tilting the head angle
By turning the adjuster knob, the tilt angle of the head can be variably adjusted between 0 and 90 degrees to suit the package content. For example, when packaging powders, tilting down the sealer head will allow the sealing to complete without powder spilling from the bag opening.


Integrated exhaust system
The exhaust air from both the driving compressor and the vacuum pump is released from the machine through a 5-meter (16 feet) 12⌀ tube.
Disconnection alarm
In the event the heating element is disconnected, the LCD screen on the microcomputer controller will alarm the user.