V-610G Series
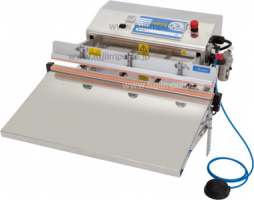
Electric-powered tabletop gas-flushing and vacuum sealers with heat temperature control.
Different options for vacuum pump available. Operates using the solenoid-drive system. Compact tabletop model capable of creating a vacuum-seal width of 61cm (24 inches).


The picture shows the nozzle extended at 0mm.

The picture shows the nozzle extended at 80 mm (maximum extension).


Main Features
Applications & Features | Tabletop/electric gas-flushing and vacuum sealer |
Operating method | Electric, solenoid-drive system |
Packaging type | Seal only, vacuum, vacuum & gas-flushing |
Daily use frequency as model selection guideline | 1,000 bags, electric |
Bag size (max.) | 61cm / 24 inches |
Latest type | Type A |
Compatible packaging materials (total thickness of two or more sheets):
Single-side heating type:
- PE : 0.3mm/11.8mil
- PP : 0.3mm/11.8mil,
- NY : 0.3mm/11.8mil,
- PVA : 0.3mm/11.8mil,
- Other laminated materials : 0.3mm/11.8mil
Double-side heating type:
- PE : 0.4mm/15.7mil
- PP : 0.4mm/15.7mil,
- NY : 0.4mm/15.7mil,
- PVA : 0.4mm/15.7mil,
- Other laminated materials : 0.4mm/15.7mil
Overview of V-610G series
The V-610G series are tabletop vacuum sealers capable of vacuum and gas-flush sealing.
- When you want to flush the air inside the bag and reduce the package volume, or when you want to utilize oxygen scavenger to extend product life, you can use the vacuum sealing function.
- When you want to fill the bag with nitrogen gas to prevent oxidation, or with carbon dioxide to create bacteriostatic or insect-repellent effects or to prevent spoilage and mold growth, you can use the gas-flush sealing function
All V-610 sealers come equipped with the ONPUL heating temperature control system that allows users to set and maintain an ideal heating temperature, and have an easy-to-maintain solenoid-drive system. They are also compact and allow you to achieve reliable vacuum seals and packaging with a simple operation.
In addition, you can choose the vacuum generator and adjust the length of the vacuum nozzle according to your situation and purpose.
Additional feature: gas-flush sealing
The series has a vacuum sealing function that can be used for flushing the air inside the bag to reduce the package volume, or to utilize oxygen scavenger to extend product life.
In addition, the V-610G has a function to flush nitrogen gas (to prevent oxidation) and CO2 gas (for bacteriostatic or insect-repellent effects and to prevent spoilage and inhibit mold growth).
Different options for vacuum pump available.
You can choose from three different types of vacuum generators based on your specific purpose and environment.
Easier maintenance with a solenoid-drive system
These sealers are equipped not with an air-drive system but a solenoid-drive system that makes use of electromagnetic force.
Benefits of using the solenoid-drive system include:
- No filter maintenance work because the air-drive system is not equipped with a dry filter※, which requires periodic replacement, thus reducing everyday maintenance work.
- No costs for an external air piping system to feed air, and reduced costs for purchasing parts that require periodic replacement, as there is no dry filter that need to be replaced.
The solenoid-drive system not only makes maintenance easier, but allows you to reduce the total cost, including those for maintaining the machine and the sealer.
Dry filter is needed for the air-cylinder-drive system because some compressed air generated by the compressor turns into water droplets, which must be removed with the dry filter.
Use of I-heating element
Use of I-heating element, which expands relatively little when heated, reduces the chance of the heating element breaking in the middle. Its use also prolongs the life of peripheral components such as the temperature sensor that comes in contact with the heating element.
Adjustable nozzle length
To accommodate vertically long bags, the length of the nozzle can be adjusted in eight-step 10 mm increments from 10 mm to 80 mm.
From the left, pictures show the nozzle completely retracted, the nozzle extended at 40 mm, and the nozzle extended at 80 mm.



ONPUL
- Seal heating temperature: 60 to 250ºC/ 140 to 480˚F
- Seal cooling temperature: between 40ºC/100˚F and the seal-heating temperature
Setting the ideal sealing condition
The most prominent feature of the ONPUL system is the ability to set the ideal sealing condition.
The heating temperature setting is made possible through the use of a high-sensitivity temperature sensor for temperature control, and a microcomputer controller.
Regardless of the air temperature or the temperature fluctuations in the machine, the ONPUL system enables you to set and maintain the heating temperature just right for melting film. As a result, the ONPUL system is energy efficient, improves the sealing precision, and reduces the wear on parts such as the heating element.
Easy-to-operate microcomputer controller
The microcomputer controller is used to select the work method and vacuum method, and to set sealing conditions. The touch screen makes the setting easy, and the LCD screen allows you to review the setting as needed.

Switch among 13 different sealing methods
The following sealing methods can be combined to create a total of 4 different sealing methods. Select a sealing method to meet your needs, including selecting to best suit the characteristics of the packaged material and to obtain your desired packaging finish.
-
Work method options
- Multiple gas flush cycles
- Vacuum + Seal
- Seal only
-
Vacuum method options
- Vacuum gauge (0 to −100kPa)
- Vacuum timer (0 to 99.9 seconds)
- Manual operation
-
Gas-flush method options
- Multiple flush cycles (up to 99 times)
- Single gas flush
- Circulating gas-flush : Set one of the two nozzles for vacuuming and the other for gas flushing. This will increase the gas-replacement rate by de-airing the bag even as the bag is being filled with gas. Especially effective with soft contents.
- Gas flushing timer setting (setting range: 0 to 99.9 sec.)
Details of 13 different sealing methods:
- Seal only
- Vacuum by manual + Seal
- Vacuum by timer + Seal
- Vacuum by vacuum gauge + Seal
- (1 time) Vacuum by manual + Gas flushing + Seal
- (1 time) Vacuum by timer + Gas flushing + Seal
- (1 time) Vacuum by vacuum gauge + Gas flushing + Seal
- n-times Vacuum by manual + Gas flushing + Seal
- (n-times) Vacuum by timer + Gas flushing + Seal
- (n-times) Vacuum by gauge + Gas flushing + Seal
- Vacuum by manual + Circulating gas flush + Seal
- Vacuum by timer + Circulating gas flush + Seal
- Vacuum by vacuum gauge + Circulating gas flush + Seal
Register up to 10 work patterns
The user can register up to 10 customized work patterns. By calling up a registered pattern on the microcomputer controller, the user can always perform a programmed work under the same condition.
Troubleshooting using the help function
Switch to the Maintenance Mode on the LCD screen to see any troubled spots on the machine indicated by a blinking light. This function enables an early detection of problems that need to be addressed.

Circulating gas-flush method
With one nozzle set for gas flushing and the other for vacuuming, the circulating gas-flush method increases gas-replacement rate by de-airing the bag even as it is being filled with gas.

Ordinary gas-flush method
Vacuuming and gas flushing are two separete processes

Adjustable table height and angle
The height and angle of the table, which comes standard-equipped, can be adjusted to suit the package content.
Standard-equipped with air filter
All V-460 sealers come with an air filter that removes moisture, fine powder, and foreign objects that are suctioned through the nozzle.